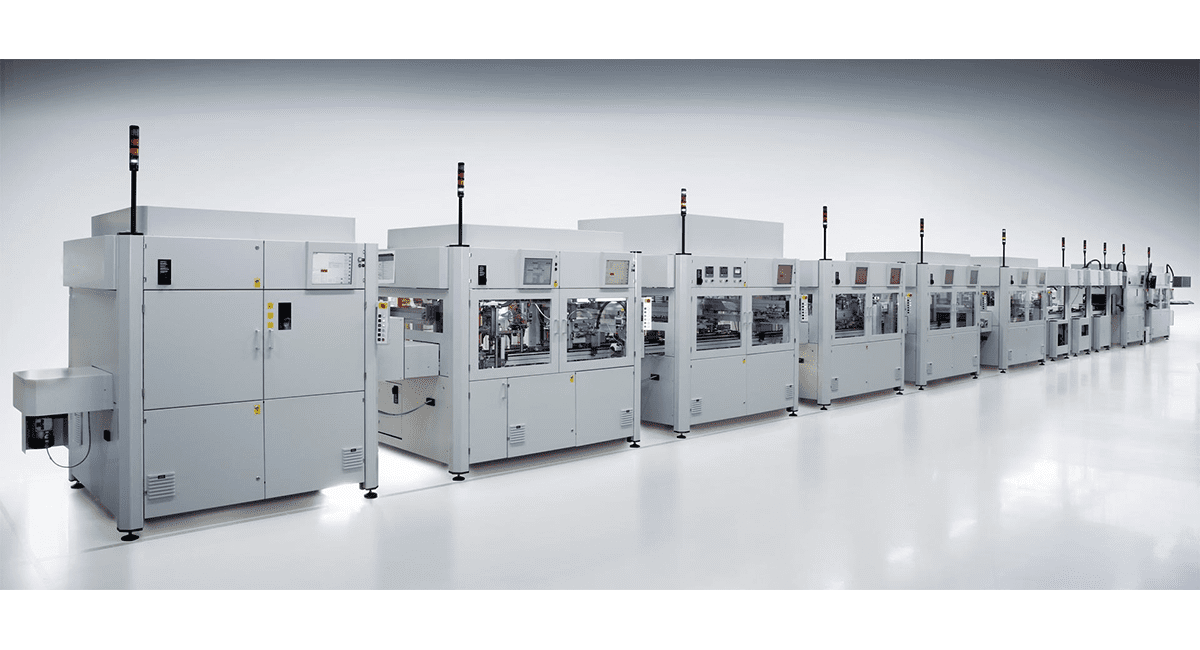
Sponsored by Schuler.
After buying the Italian Sovema Group, Schuler is regularly establishing itself as a system provider within the subject of battery manufacturing. The primary profitable large-scale tasks present that the technique is working.
Schuler handed an essential milestone as a provider for gigafactories with the development of a formation line for a big German battery cell producer. After the deliberate begin of manufacturing in Could 2025, the road will be capable to produce round 80 cylindrical lithium-ion cells per minute. Along with planning, manufacturing, and assembling the road, Schuler has additionally taken on your entire intralogistics, the metal development, and the implementation of digital options that embody a track-and-trace performance for the plant.
The rising enterprise exercise, that Schuler has solely not too long ago developed for the manufacturing areas of cell meeting and formation, follows a clearly outlined technique. The ANDRITZ Group, because the mother or father firm of Schuler, has elevated battery manufacturing for the electromobility sector with a complete of seven progress tasks. The aim: assist battery makers produce aggressive batteries in Europe and America.
Step one was the acquisition of the Italian Sovema Group in August 2022. Within the automotive sector, Sovema made a reputation for itself over the previous ten years as a system provider for pilot and laboratory tasks within the subject of lithium-ion batteries. As well as, the corporate is taken into account a number one international supplier of turnkey techniques for the mass manufacturing of lead-acid batteries. The US subsidiary Bitrode additionally contributes extra tools and know-how within the subject {of electrical} battery testing of cells, modules, and packs.
With Sovema’s experience and expertise, Schuler is ready to cowl your entire manufacturing line within the cell meeting and cell ending areas: the notching and stacking processes, manufacturing of housing elements, and filling of electrolytes from formation to ageing to remaining sealing.
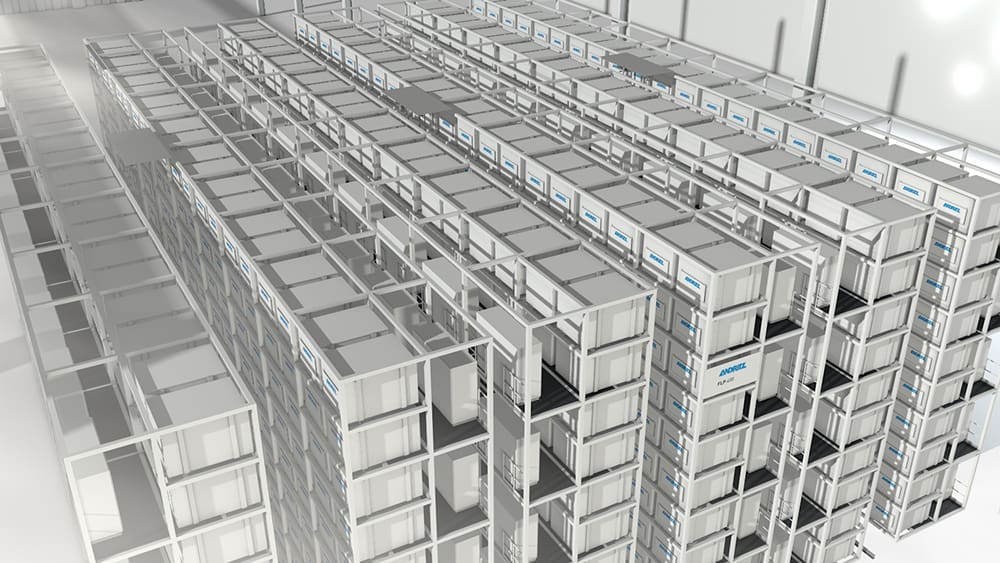
Schuler can develop the meeting and formation manufacturing traces and scale them up for the mass manufacturing of battery cells. Earlier than the takeover, Sovema primarily manufactured laboratory and pilot techniques.
By way of course of expertise, Schuler can draw by itself experience within the manufacturing of prismatic and cylindrical battery cell housings (“Can & Lid Manufacturing”), for which it has been constructing crops since 2015. Within the subject of cylindrical cell housings, the Göppingen-based firm not too long ago delivered 4 absolutely automated turnkey manufacturing traces for a world-renowned carmaker in Germany and the USA. One other line for the manufacturing of prismatic housings, with a manufacturing velocity of 100 housings per minute, went to Hungary.
Experience and capacities from different enterprise areas of the ANDRITZ Group can be found. For instance, the group has been manufacturing centrifuges for lithium mining because the Nineteen Sixties and in addition affords filter and drying techniques which are wanted in powder processing for the manufacturing of lively cathode materials. ANDRITZ additionally has intensive know-how in calendering processes, the place rolls are used. Final, however not least, ANDRITZ’s personal recycling division contributes intensive data and expertise within the areas of dismantling, deep discharge, and recycling of batteries. The main focus right here is on developments over the subsequent 5 to 10 years, when rising gross sales figures will imply that an increasing number of manufacturing waste from used electrical automobiles must be recycled.
In November 2022, Schuler acquired an order from the Fraunhofer Analysis Establishment for Battery Cell Manufacturing FFB at its Münster website to design a cell meeting line for large-format pouch cells in three totally different lengths. One other main venture is presently underway for certainly one of Germany’s main automotive producers. The main focus of this venture is the development of a pilot cell meeting line for the manufacturing of revolutionary “solid-state” battery cells. In comparison with standard lithium-ion batteries, these solid-state cells have plenty of market-relevant benefits. These benefits relate to essential security elements (not like lithium-ion batteries, solid-state batteries can not catch fireplace); they’ve increased power density than lithium-ion batteries and may generate a considerably better vary for electrical automobiles. Shorter charging occasions are one other important benefit in terms of assembly probably the most demanding necessities within the subject of electromobility. The turnkey handover of the plant for this main venture is scheduled for Could 2025.
Dr. Hermann Uchtmann, Head of Schuler’s “Battery Giga Tasks” enterprise unit, notes the explanations behind present market restraints for plant producers within the subject of battery manufacturing: “Taking the present gross sales figures for electrical vehicles as a place to begin, the battery marketplace for automotive purposes is in a section the place the exaggerated expectations have arrived within the ‘trough of disillusionment.’ We count on demand to choose up considerably once more within the coming years. We’re utilizing the time successfully to optimize our merchandise for gigafactory traces within the space of battery cell manufacturing for market demand.”
However to what extent can Schuler seize the market share from opponents within the Far East? For these in cost, probably the most highly effective arguments listed below are straight linked to the core ideas of innovation, high quality, and effectivity. Uchtmann states: “Sooner or later, we need to make better use of our revolutionary edge within the subject of plant expertise, significantly within the space of large-scale manufacturing. That is related for a goal group, such because the automotive sector, which locations the best calls for on manufacturing. That is how we are able to mix our excellent high quality options and the particular cost-effectiveness of our techniques into a standard denominator.”
In battery cell manufacturing, the excessive manufacturing high quality is mirrored, above all, in low rejection charges. One other essential issue, particularly for the German market, is the bottom attainable power consumption that’s measured towards the consumption values of opponents. Uchtmann says: “Right here, for instance, we are able to obtain excessive power effectivity values of virtually 90 % utilizing the formation electronics we make use of.” In keeping with Uchtmann, additional financial savings will be made by minimizing the house required, particularly the place excessive prices can come up for the operator—akin to working drying rooms.
For Uchtmann, the companies that accompany the plant development clearly communicate “professional Schuler.” “A decisive benefit is that our crops are predestined to be used within the European market. Not like in Asia, European battery cell producers are accustomed to having their crops delivered, assembled on-site, and arrange prepared for operation. Added to this are the dependable upkeep and restore companies that we offer within the after-sales sector, together with extremely dependable spare elements deliveries. It’s right here, within the continued productiveness and availability of the plant, that our experience actually pays off: the client then has a companion at their facet that they’ll depend on!”
Study extra at www.schulergroup.com.